05 Dec Let you know about Cutting and Annealing Machine at one time
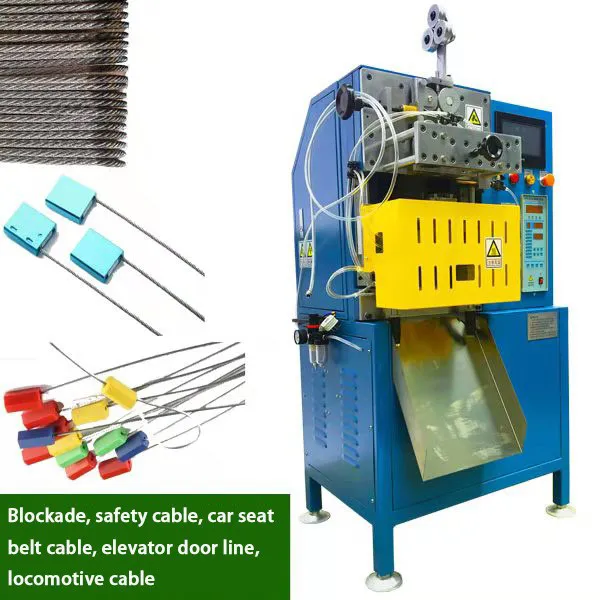
1.Cutting and Annealing Machine workflow
Today we will let you know the cutting and annealing machine at a time.
First, Manual, or fully automatic operation start.
↓
During the feeding stage, the conveying motor completes the feeding according to the input length
↓
Fuse function is triggered when the feeding is completed.
The upper clamp is tightened and the lower clamp is tightened (pre-pressing time)
↓
The first stage of tightening motor operation is heated by current (preheating time, preheating heat)
(Visually let the wire rope heat up to a red state, but not shiny)
↓
First stage of tightening motor continues to run and preheating stops .(interval time)
(In order to tighten more, but do not continue heating to prevent overheating and fracture)
↓
Heating by melting heat: The wire rope is heated to the melting point. (welding time welding heat)
The stretching cylinder works, and the tightening motor runs in the second stage. Before the wire rope melts, it is pulled down to form a cone head and melts at the same time.
↓
When the lifting cylinder reaches the bottom, the chuck is released (pressure holding time ends) and the stripping auxiliary chuck works.
↓
The photoelectric detection device detects the material shedding situation, and enters the next cycle of work if it is normal.
2.Precautions when using the machine
Things to note before operation:
- Please confirm whether the electrical and air pressures are normal.
- Please confirm whether the upper and lower chuck heads are correct and whether the slide rails are smooth.
- Please confirm whether there are foreign objects on the equipment.
- Please confirm whether the material feeding is smooth and there should be no resistance when pulling the wire rope to feed.
- After confirming that it is normal, start the equipment, turn on all electrical switches, and manually operate the equipment to observe whether it is running normally.
- After the equipment is started, manually produce and automatically produce, and check that all functions are normal and the products are qualified.
Things to note during operation:
- After starting the electrical switch, do not put your hands into the upper and lower clamps.
- When the equipment is running to feed wire, do not put your hands into the wire feeding wheel, and do not drag the wire rope with your hands.
- After the equipment is running automatically, do not cover the photoelectric detection position of the discharge port.
- Press the emergency stop switch in time when encountering feeding abnormalities or other abnormalities.
- Please wear protective equipment (such as protective goggles, etc.) when debugging the equipment or observing the fusing effect at close range.
- When taking or sorting the fused product, please wear heat-insulating gloves or use tools to grab it to prevent burns.
Things to note after the equipment stops running:
- After the equipment stops running, please turn off the power switch on the panel first, and the indicator light will go out.
- Turn off the power switch on the fuse controller, and the number on the controller will go out.
- Cut off the power supply of the air switch in the electrical box or the external switch.
- Cut off the air pressure, close the external air pressure valve or pull out the air pipe joint.
- Loosen the wire feeding pressure device and pull out the wire rope.
Equipment Installation:
- When installing the equipment, pay attention to adjusting the height of each foot to keep the equipment level. The installation site should pay attention to the necessary space for equipment operation, maintenance and repair. (Please refer to the size of the wire coil used for production and the way of wire outlet).
Equipment Lubrication:
- The equipment operation and sliding parts (such as conductive copper plates, sliding chucks) need to be filled with oil once a week;
- Grease (nitro grease) should be injected into the gear meshing parts once every fifteen working days.
- The linear bearings are filled with oil according to the working hours, and generally once every fifteen working days.
3.Cutting and Annealing Machine Purpose
Cutting and Annealing Machine is designed and manufactured by Baoding Zunzz Machinery Co., Ltd. It is designed mainly for the production and processing industries of various lead-sealed wire ropes, lock wire ropes, sealing strip wire ropes, locks, etc., to sharpen the wire ropes after melting and solve the problems of unstable quality, numerous processes, and increasingly serious labor difficulties in manual processing. It can also save manpower and multiple processes to reduce production costs and increase production capacity. It is a fully automated equipment that can be managed by one person at the same time.
This equipment is widely used in the automatic cutting of wire ropes of any specifications in the medical equipment, auto parts, building safety, office furniture, bicycles, sports equipment, locks, etc. High-precision touch-type full computer control system, easier setting and change of fusing conditions, and good fusing quality can be obtained.
If you want to know more about Cutting and Annealing Machine, or have any questions about the equipment, you can send us your requirements at any time.