14 Dec Ten major faults of wire rope swaging machine
Detailed analysis of the top 10 problems that may occur during the use of the machine, and provides practical solutions.
1. The pressure of the swaging machine cannot reach
When the wire rope swaging machine is working, the pressure will drop after it rises. What causes this failure?
- The main overflow valve in the hydraulic system of the swaging machine is seriously worn, resulting in overflow and debris, and is stuck, so the pressure cannot rise;
- The flushing valve on the upper part of the swaging machine cylinder is not opened, so it cannot rise normally;
- The oil pump flow is abnormal, such as the pump flow and pressure become inversely proportional, which will also cause the hydraulic pressure to fail to rise;
- The lower chamber directional valve of the hydraulic system is stuck, and the oil also enters the upper and lower chambers;
Failure in the circuit of the swaging machine will also cause the hydraulic pressure to fail to rise. Use a screwdriver to poke the small reversing valve to see if it is stuck. And then test whether the indicator light of the rising small valve is on; - The valve core of the filling valve of the hydraulic system is stuck due to debris or springs, which will also cause the hydraulic pressure to fail to rise;
- The cartridge valve and reversing valve in the hydraulic system of the sleeving machine are stuck;
2. Wire rope swager bearing damage
Wire rope swager are often used to press wire ropes, but the bearings of the swaging machines may be damaged during long-term use. What causes this?
- The bearing seat or bearing hole is poorly processed, which may cause poor fit between the bearing and the hole, causing bearing damage.
- The bearings of the wire rope are not fully lubricated in time during long-term use, which will increase bearing friction and cause bearing damage.
- When replacing new bearings, the bearing position is not paid attention to, resulting in tilting or twisting of the bearings, which will cause bearing damage during use.
- The environment in which the hydraulic swaging machine is used is relatively harsh, such as using it in a highly corrosive environment, which causes corrosion on the bearing surface and causes bearing damage.
The above are the reasons for bearing damage. Of course, it is recommended to contact the manufacturer when replacing the bearing to avoid damage to other parts of the swaging machine during the replacement process.
3. Control panel failure
During long-term use, some users may encounter malfunctions in the control panel of the swager, which will not only affect production efficiency, but also cause damage to the equipment. So what causes the malfunction of the control panel of the wire rope swaging machine?
- Unstable power supply or excessive or low voltage may cause the control panel to malfunction. In addition, problems such as poor contact of the power line and damage to the power switch may also cause control panel failure.
- If the components on the control panel, such as buttons, switches, and indicator lights, are damaged or aged, the control panel may also malfunction.
- If the core program of the hydraulic wire rope swaging machine is wrong or damaged, the control panel may malfunction. When the swaging machine program fails, the control panel may also malfunction.
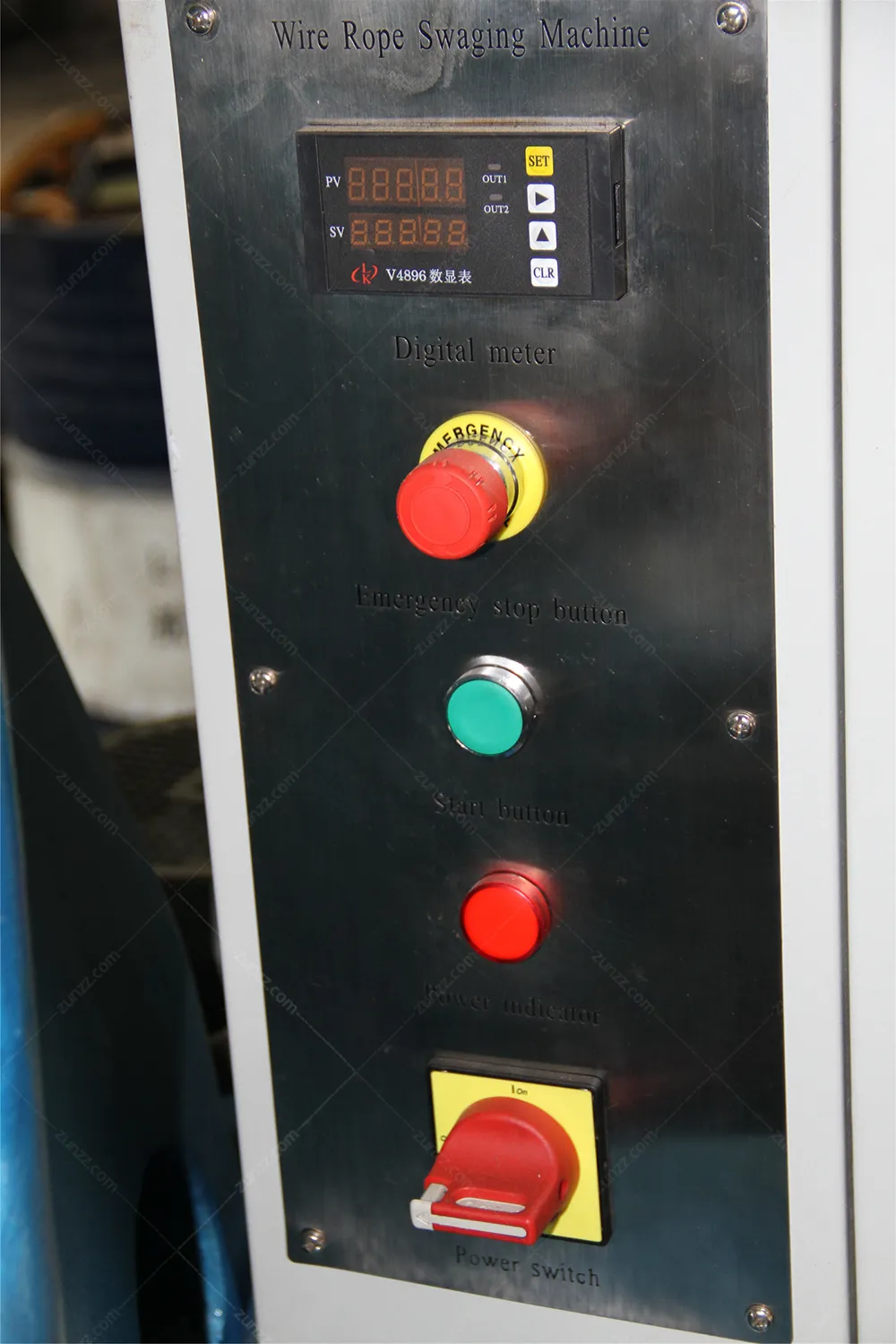
Source: Wire Rope Pressing Machine
4. Cylinder block burst
Some operators encountered cylinder explosion accidents when using the swager. What caused this?
After inspection, it was found that the main reason for the explosion of the swager cylinder was the aging of the equipment, and the aging cylinder of the equipment was seriously worn and corroded, resulting in a decrease in the strength of the cylinder, which led to the explosion accident.
In addition to the aging of the equipment, inadequate maintenance is also one of the main reasons for the explosion of the cylinder. Because the wire rope swaging machine is a high-strength equipment with a high frequency of use, it needs regular maintenance and maintenance. If the maintenance is not timely, it will cause the equipment to age, resulting in deformation and explosion of the cylinder.
5. The wire rope swaging machine does not move upward
In addition to improper operation by the operator, the following are several other reasons for the problem:
- The mobile motor is damaged.
- The gear of the high-speed shaft from the mobile motor to the reducer is damaged.
- The reducer is damaged.
- The one-way valve inside the hydraulic oil pump is damaged.
- The oil pipe is blocked or the oil pipe bursts. If the flow rate of the pump is inversely proportional to the pressure, it will also cause the hydraulic pressure to fail to rise.
- The internal pressure of the oil cylinder is released, such as the valve core of the hydraulic system’s filling valve is stuck due to debris or springs, which will also cause the hydraulic pressure to fail to rise.
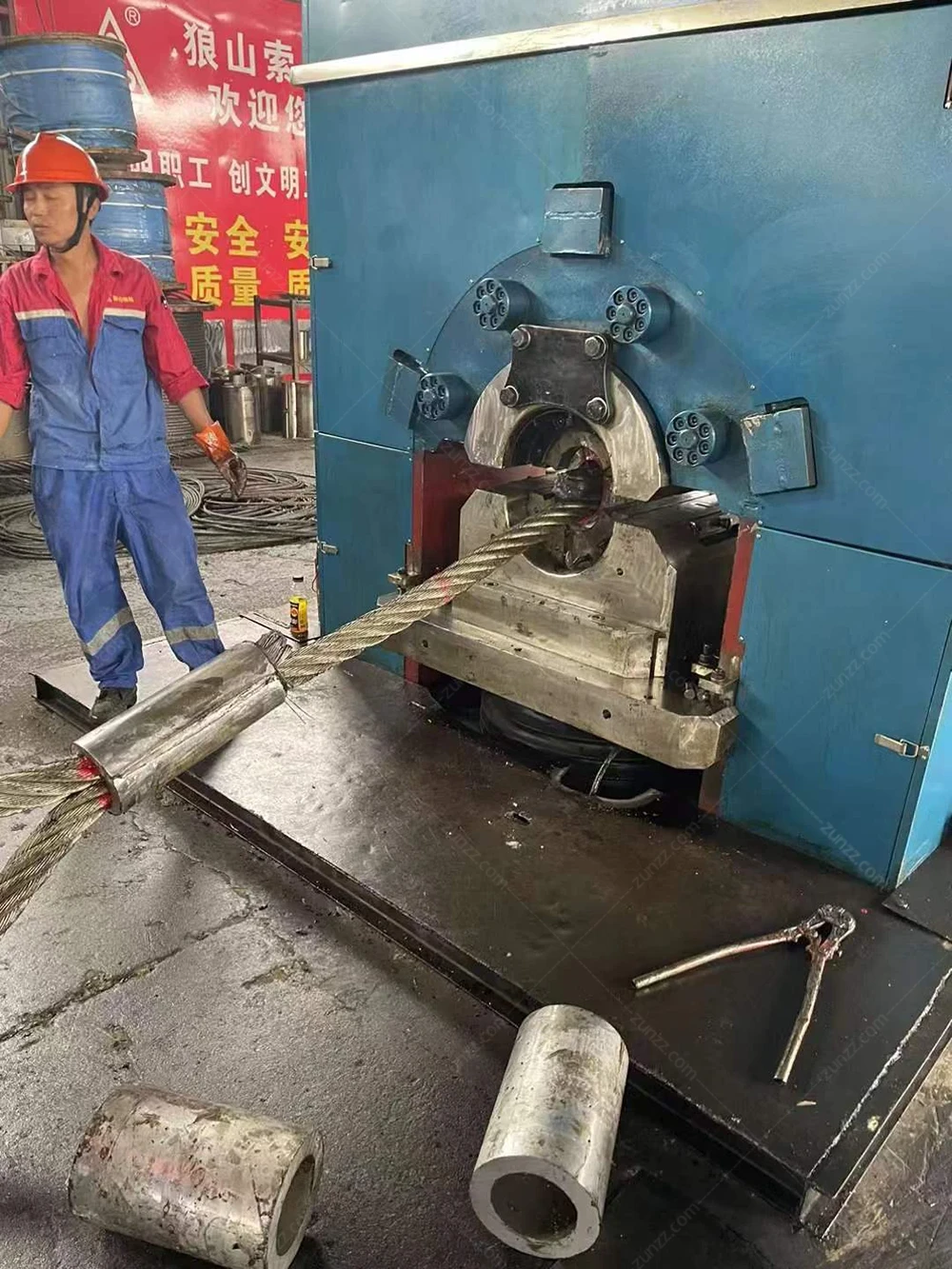
Source: Wire Rope Swaging Press
6. Too much noise
The noise of the wire rope swager is too loud. First, analyze whether the noise comes from the motor or the oil pump.
The possible problems of the motor noise are:
- One phase voltage is too low and the three phases are unbalanced.
- The motor is missing phase.
- Motor quality problem.
The possible problems of the oil pump noise are:
- The hydraulic oil pump is worn or sucked.
- The oil viscosity is too high, resulting in cavitation and cavitation, making the oil pump difficult to operate.
- The oil contains mechanical impurities, which accelerates the wear of hydraulic components and causes hydraulic system failure.
- The oil inlet filter is seriously polluted and blocked.
The noise can be reduced according to the following methods:
- Check the wear of the hydraulic pump
- Appropriately reduce the viscosity and select hydraulic oil whose viscosity is less affected by temperature difference. At normal temperature, Zunzz Machine recommends the use of 46# anti-wear hydraulic oil. In areas with relatively low temperature, relatively low hydraulic oil can be used accordingly. In areas with relatively high temperature, 46#+ hydraulic oil can be used.
- Replace the oil
- Clean the oil inlet filter.
7. Motor overheating
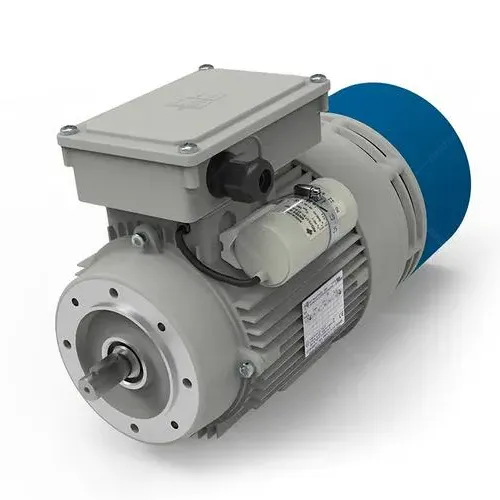
There are several reasons for motor overheating.
- Analyze the motor overload situation. Use a clamp meter to measure the normal current of the motor. If the current of the motor load is sometimes large and sometimes small, it may be that the hydraulic pressure is increased; if the current is relatively large when the machine is just turned on, and the current of the hydraulic system is too high before it starts running, it means that there is a problem with the motor.
- Check whether the bearings of the motor of the hydraulic system are stuck and the rotor is swept, because when such a fault occurs, the operating technicians can generally hear the sound.
- The voltage fluctuation of the external power grid becomes larger. Use a multimeter to check it first and it will be clear immediately. Perhaps it is caused by the large resistance of the hydraulic pump, the mismatch between the motor and the pump, the decrease in motor insulation, and the reinstallation after disassembly.
8. Motor thermal trip
Several solutions to tripping
- Adjust the pressure value of the overflow valve.
- Repair the valve blockage.
- Repair the check valve.
- Repair or replace the motor.
9. Oil temperature is too high
If the oil temperature of the wire rope press machine rises too high during normal use, you should be alert. Generally, in this case, there must be some minor faults somewhere, so the swager should be stopped first and then checked. There are several reasons for the high oil temperature:
- Poor heat dissipation of the system. The oil tank is too small during design and selection, causing the oil to circulate too quickly, or the cooling system is not used due to high ambient temperature, or the cooler is used but the cooler effect is poor. These are all reasons for poor heat dissipation.
- Poor operation of the hydraulic system unloading circuit. Usually, an unloading valve is set at the pump outlet of the system. When the system is not loaded and does not need pressure oil, the system is unloaded to reduce energy loss. If the unloading valve does not work properly, the oil will still overflow from the overflow valve back to the oil tank when pressure oil is not needed, which will increase the oil temperature.
- Impact during the hydraulic system switching and speed switching.
- Serious leakage in the hydraulic system. Most people think it has nothing to do with temperature rise. As we all know, leakage will cause energy loss. So what is this energy loss converted into? In fact, they are all converted into heat energy, which increases the oil temperature.
- Air or water enters the hydraulic oil. When the hydraulic pump of the hydraulic press converts the oil into pressure oil, if there is air and water, the heat will increase and cause overheating.
- Misuse of hydraulic oil with too high viscosity or hydraulic oil becomes thicker. Oxidation of hydraulic oil or low ambient temperature will increase viscosity. Hydraulic oil with too high viscosity will increase friction and cause heating.
10. Large vibration during operation
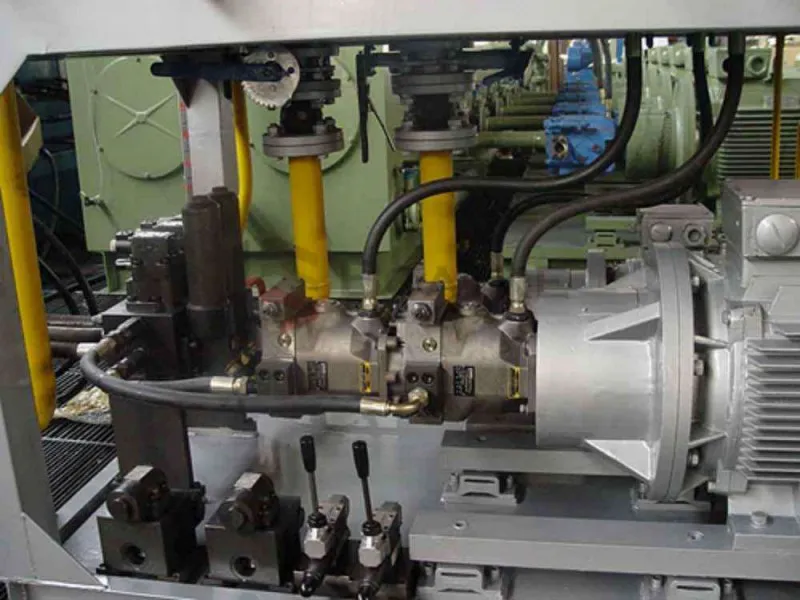
Vibration is the most common fault in the hydraulic system of hydraulic equipment and one of the three major chronic diseases. The impact caused by the high-speed flow of hydraulic oil in the pipeline and the impact caused by the opening and closing of the control valve are the causes of vibration in the system. Strong vibration will cause errors in system control actions and some more precise instruments in the system to make errors, leading to system failures.
Solutions:
- The hydraulic pipeline should be fixed as much as possible to avoid sharp bends.
- Avoid frequent changes in the direction of the fluid flow. If it cannot be avoided, vibration reduction measures should be taken.
- The entire hydraulic system should have good vibration reduction measures, and at the same time, the influence of external vibration sources on the system should be avoided.
If you have more questions about the wire rope swaging machine, or have any questions and needs about the equipment, you can send us your requirements at any time.