24 Sep Wire Rope Slings Classification
1. PRESSED STEEL WIRE ROPE RIGGING
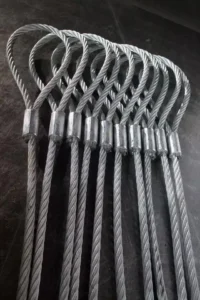
Pressed rigging is a type of steel wire rope sling that we commonly use, which is generally divided into two types: with a collar and without a collar. Compared with old-fashioned steel wire rope slings, press rigging has a more novel structure, more advanced technology, and higher production efficiency. It has strong safety and reliability, high load, and strong consolidation of press joints. The joint surface is smooth, without cracks, flash edges, and burrs, making it very suitable for various professional production occasions.
2. SPLICED STEEL WIRE ROPE RIGGING
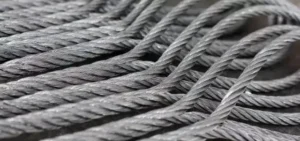
Splicing steel wire rope rigging is the process of machining one or both ends of a steel wire rope into a circular shape through insertion. Compared with pressed steel wire rope rigging, spliced steel wire rope rigging is cumbersome in operation and relatively backward in technology. Each spliced rigging consumes more steel wire rope, resulting in higher costs. Additionally, the spliced head has weaker consolidation than pressed rigging, making it commonly used in specific occasions such as steel, chemical, and other industries.
3. JOINT LESS STEEL WIRE ROPE LOOP
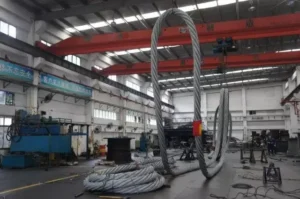
The significant characteristics of non joint rigging are good flexibility, multiple lifting points, high strength, and small lifting space requirements. It is particularly suitable for lifting large objects in limited space or oversized lifting projects, such as transformers, shipbuilding, and special machinery manufacturing environments.
4. CAST STEEL WIRE ROPE RIGGING
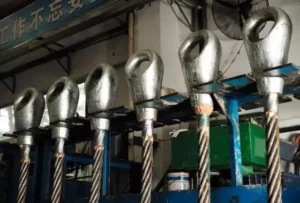
The casting process manufacturing is complex, and operators also need to undergo training before casting. Manufacturing requires a certain amount of time, low efficiency, and high cost. However, the solidification strength of casting rigging is high, and it is often used in important occasions. There are many on-site casting installations, and tensile testing is required before leaving the factory every time.